Interviews Vol. 1 – The Hazara Redesign (Part 1)This is the second part of our interview about the redesign of the Hazara leaf-shaped plate in 2021.
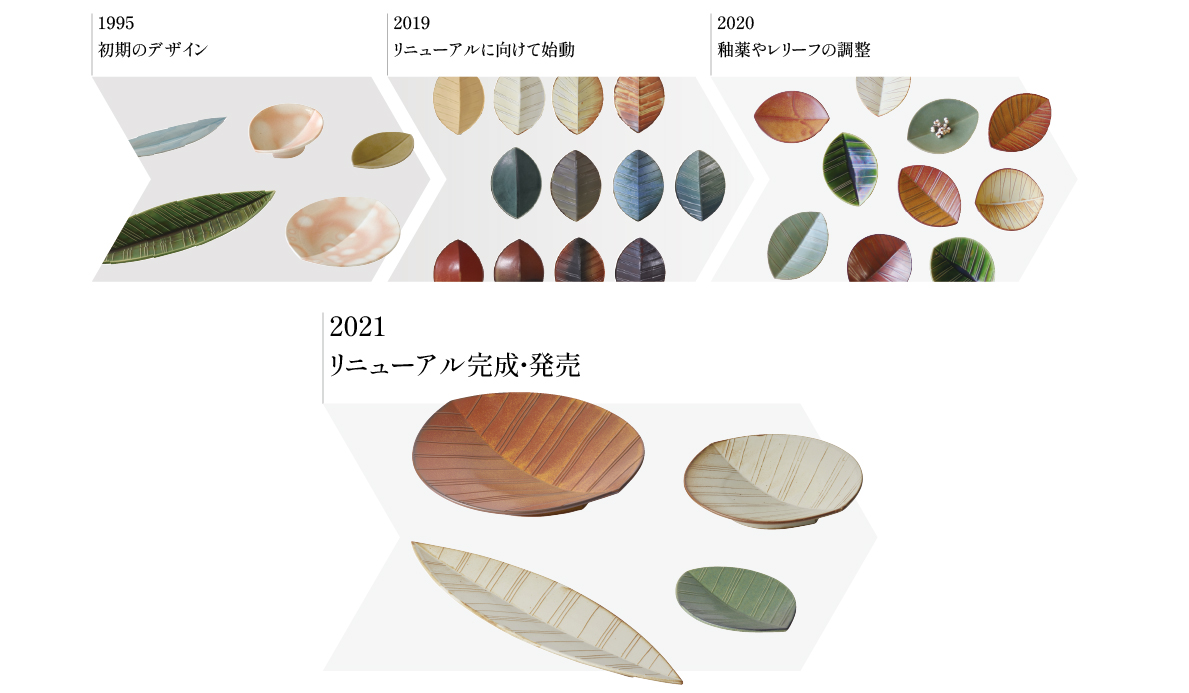
When it was first released in 1995, the Hazara series by Ceramic Japan was produced with numerous traditional glazes using a design that gave off an atmosphere of Japanese style tableware. Then, in 2019, a proposal was made to exhibit the Hazara series at a trade show overseas, and a project was launched to renew it after repeated discussions with the designer, Makoto Komatsu. After repeatedly testing different relief effects and glazes, it was decided to produce the series with three glazes that transform during firing.
-
Sabicha
Sabicha, or rusty brown, is a color used in Japanese paintings that comes from a category of mineral pigments. The motif of the color is the rust that occurs on metals. The Sabicha glaze used on the Hazara series creates a beautiful transformation from yellow to red, then red to brown, much like autumn leaves. When the edges stand out from the many variations of the reddish brown glaze, it gives a sharp impression.
-
Hakushu
The Five Elements is a natural philosophy born in ancient China. In that philosophy, middle age in a person’s life is describe with the word Hakushu. The Hakushu glaze in the Hazara series is a calm color in which a bit of brown has melted into a base white color. A delicately burnt expression emerges in the spots where the glaze is particularly thin, and yellows and browns that evoke autumn are blended in.
-
Banryoku
Banryoku is a seasonal word used in Haiku poems. The word is used to describe an entire area covered with grasses and trees. The Banryoku glaze used in the Hazara series offers an appealing color with depth. The mysterious coloration that seems to mix blue, green, and yellow, is the result of wiping the base material with dye before applying glaze to give each piece a finish with greater depth.
-
Variable glaze
Variable glaze refers to the way that the color of glaze can be transformed in the kiln during firing. The mutual interaction between the constituents of the glaze with factors such as changing flame, temperature, and cooling speed, result in a piece that is different each time it is taken from the kiln after firing. The glaze embodies the concept of coincidence in each ceramic piece.
This is the story of product development at Ceramic Japan entitled Interview Vol. 1. This issue features a special on the Hazara series that was recently renewed and put back on sale. Of particular attraction is the shapes of the series. We asked numerous questions to the designer, Makoto Komatsu on the feelings for the series, such as how he arrived at the shallow V shape or why he selected variable glaze.
-
Q. What was your first reaction when you heard the proposal from Ceramic Japan to renew the series?
The renewal of the previously released Hazara series that I designed offered numerous possibilities, such changing the relief, materials, clay, or glaze. For a designer, the opportunity for their products to remain in the market for just a little bit longer by renewing their own design is quite lucky.
Nothing would give me more pleasure than for some new user to discover it and like it as a result. -
Q. What was your thinking behind choosing glazes with a different atmosphere than the original Hazara?
I chose traditional glazes used in Japanese tableware for the original Hazara series. Those traditional glazes, which have been used continuously for hundreds of years, have a certain strength and a Japanese spirit. The reason I chose a different glaze for this renewal is because I wanted the result to match not only with Japan but global cuisine as well. My hope is that the changes in clay and glaze and fire, or variable glaze, result in each Hazara piece having its own personality.
… Look forward to the continuation of this interview with Makoto Komatsu in the second half.